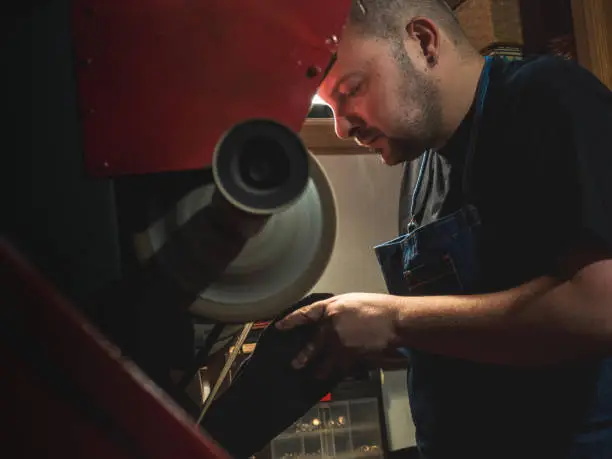
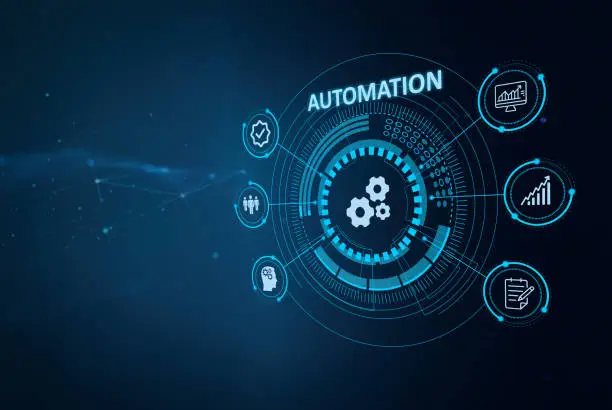
How Automation is Shaping the Future of Metal Spinning
Automation impacts every corner of modern manufacturing, revolutionising traditional processes across industries. In the world of metal spinning, a highly specialised and precise craft, automation is opening new doors to efficiency, cost savings, and enhanced quality. This article delves into how automation reshapes the metal spinning process, highlighting its benefits, addressing challenges, and exploring its future potential.
The Evolution of Metal Spinning
Metal spinning is a versatile and efficient process for shaping metal into symmetrical components. Known for its ability to produce high-quality, durable parts with minimal material waste, traditional metal spinning is a cornerstone of manufacturing for industries such as aerospace, automotive, and construction. This process relies on the skill and craftsmanship of trained operators who use their expertise to create precise and intricate designs.
Its flexibility and cost-effectiveness set metal spinning apart, particularly for small production runs or custom designs.
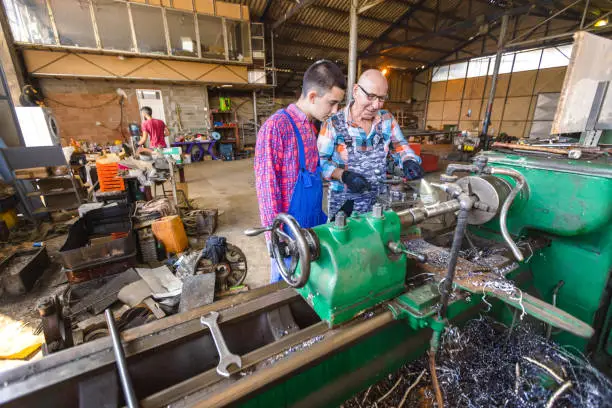
The process can accommodate a wide range of materials, from aluminium and steel to more exotic alloys, making it an invaluable method for producing components across diverse industries.
However, automation is emerging to enhance the natural strengths of metal spinning. Rather than replacing traditional methods, automation builds upon their foundation, allowing manufacturers to scale up production, achieve even greater precision, and explore more complex designs. By integrating automation into this already robust process, manufacturers are unlocking new possibilities without compromising the inherent advantages of traditional metal spinning.
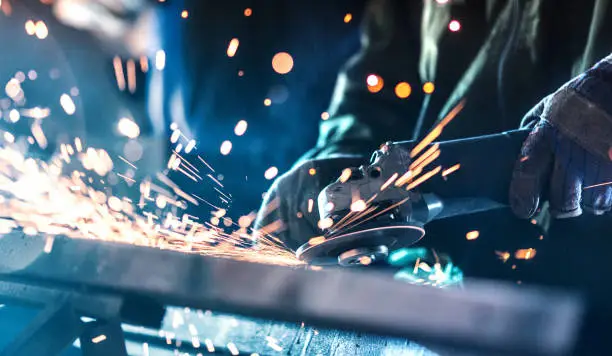
How Automation is Redefining Metal Spinning
The integration of automation into metal spinning has transformed what was once a labour-intensive process into one driven by advanced technologies. Automation leverages tools like CNC (computer numerical control) machinery, robotics, and intelligent software to streamline production while delivering unmatched precision and consistency.
These technologies work in harmony to produce flawless results:
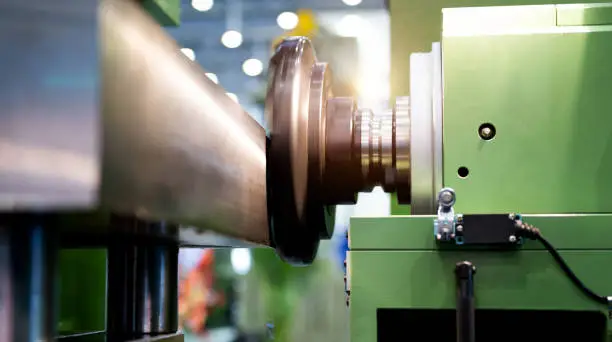
- CNC Systems: These systems allow for the pre-programming of intricate designs, ensuring that every spin adheres to exact specifications. Their precision eliminates variability and ensures consistent quality across production runs.
- Robotic Systems: Robotic arms handle repetitive and hazardous tasks such as material loading, unloading, and inspection. This addition improves safety and efficiency while minimising the potential for human error.
- Real-Time Monitoring Tools: Sensors and software continuously track performance metrics, allowing real-time adjustments that optimise the spinning process and enhance product quality.
By blending these technologies, manufacturers can achieve levels of precision and efficiency that were once unimaginable, paving the way for innovative designs and applications.
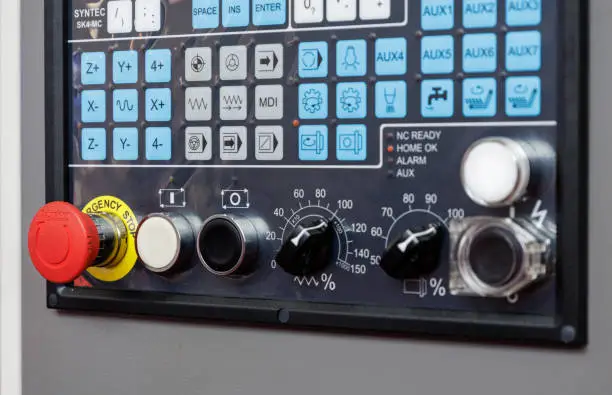
The Benefits of Metal Spinning Automation
Automation has redefined the benchmarks of efficiency and quality in metal spinning, offering benefits that permeate every stage of production. The advantages are multifaceted, transforming how manufacturers approach this craft.
One of the most significant benefits is precision and consistency. Automated systems eliminate the inconsistencies that can arise from manual intervention, ensuring that each component meets the required specifications. This level of accuracy is particularly critical in industries like aerospace, where precision is non-negotiable.
Automation also drives cost savings in several ways. Automated systems require fewer operators, reducing labour expenses, while material waste is minimised thanks to the precise control of machinery.
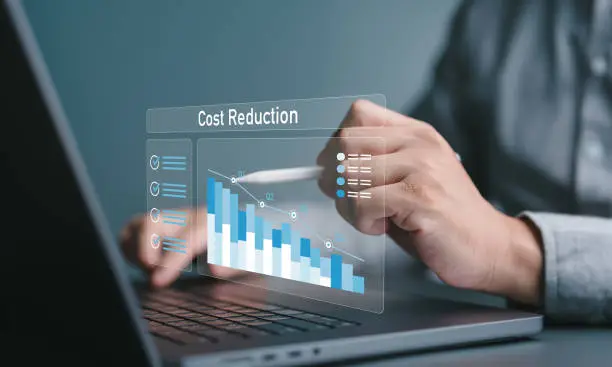
Over time, these savings significantly outweigh the initial investment in automation technology.
Additionally, productivity soars with automation. Unlike human operators, automated systems can run continuously, enabling around-the-clock production without breaks. This always-on workforce ensures manufacturers meet tight deadlines and adapt quickly to market demands.
Equally significant is the safety improvement. By automating hazardous tasks, manufacturers reduce the risk of workplace injuries, creating a safer environment for their employees. Workers can then focus on higher-value tasks, such as quality assurance and system oversight, further enhancing operational efficiency.
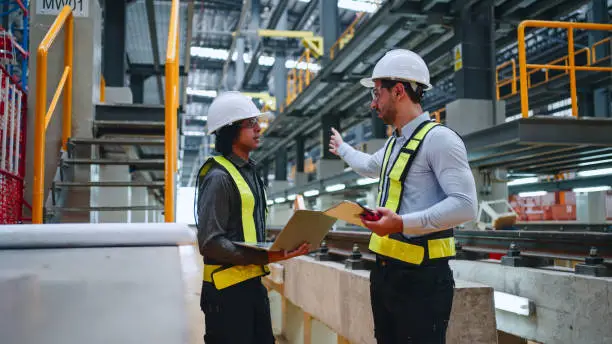
Real-World Applications of Metal Spinning Automation
The impact of automation is evident across industries that rely on precision and scalability. By streamlining production and ensuring consistent quality, automation has unlocked new possibilities in sectors as varied as aerospace, automotive, and healthcare.
- In the aerospace sector, the demand for lightweight yet durable components is ever-increasing. Automation ensures that parts such as engine housings and cones are produced with exacting precision, meeting the stringent regulatory standards of the industry.
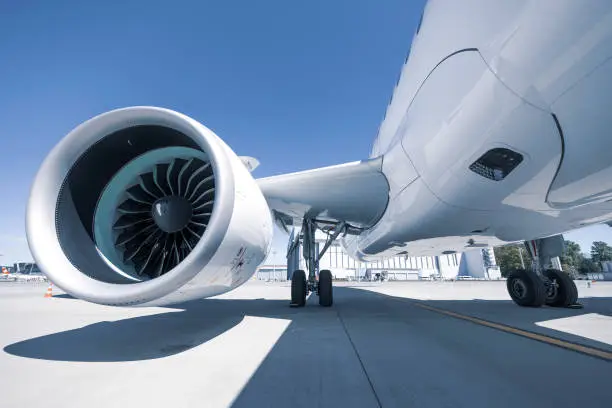
- In automotive manufacturing, speed and efficiency are paramount. Automated metal spinning systems enable the rapid production of essential components, from structural parts to decorative features, without compromising on quality.
- The medical field relies heavily on precision and consistency. Automated systems are instrumental in creating surgical instruments, implants, and other critical medical devices, meeting the rigorous standards required in healthcare.
- Even custom manufacturing has benefited from automation. Applications such as decorative metal elements or bespoke industrial components are produced faster and with higher quality, thanks to the adaptability of automated systems.
These examples illustrate how automation not only enhances current production but also sets the foundation for future advancements in metal spinning.
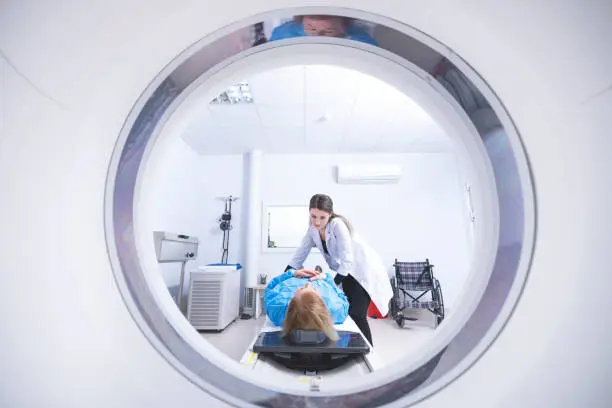
Addressing Challenges in Implementation
While the benefits of automation are profound, the path to adopting this technology is not without its obstacles. For many manufacturers, the transition requires careful planning, strategic investment, and a commitment to training and culture change.
- The initial costs of implementing automation can be daunting. High-end CNC machines, robotics, and software systems represent a significant upfront expense. However, these investments should be viewed in the context of long-term gains. Savings in labour costs, material efficiency, and reduced downtime often yield a positive return on investment within a few years.
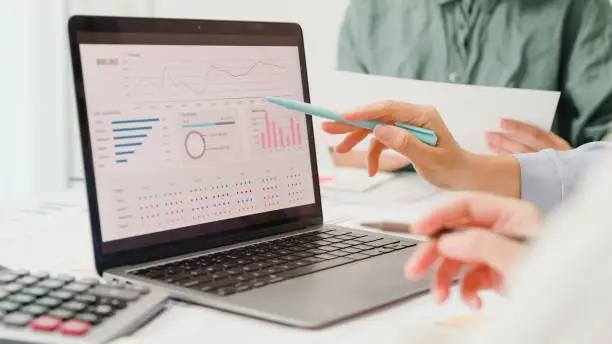
- Training requirements also pose a challenge. Automated systems demand operators skilled in programming, monitoring, and maintaining advanced machinery. Manufacturers must invest in upskilling their workforce or partnering with technology providers who can deliver tailored training programmes.
- Finally, overcoming cultural resistance is critical. Automation may be perceived as a threat to job security or as a disruptive force to established workflows. Companies can foster a culture that embraces innovation by engaging with employees and communicating the benefits—such as safer working conditions and opportunities for higher-value roles.
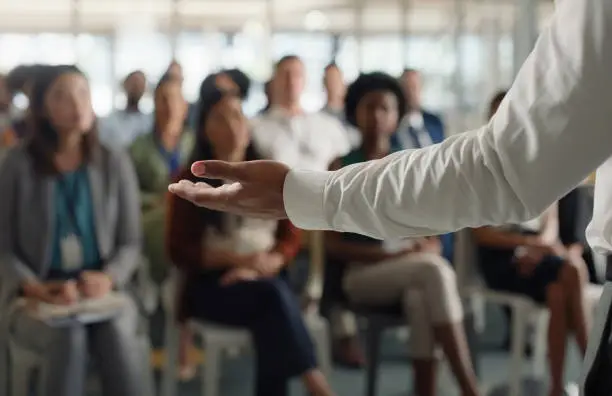
Unlocking the Potential of Automation in Metal Spinning
Automation is not just transforming the metal spinning process but redefining what is possible in manufacturing. For companies seeking to remain at the forefront of their industries, embracing automation is about more than just efficiency—creating opportunities for innovation, sustainability, and growth.
As a leader in metal spinning, Tanfield Metal Spinners understand the delicate balance between honouring the craftsmanship of traditional methods and adopting the technologies that will shape the future. Automation enhances the strengths of metal spinning, enabling us to achieve levels of precision, productivity, and customisation that were once out of reach.
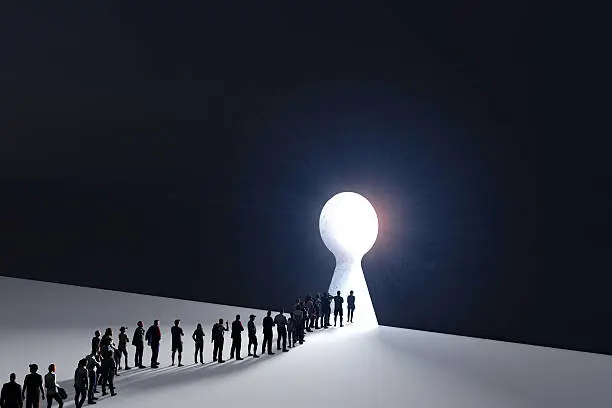
Our commitment to innovation and expertise positions us at the forefront of this transformation. We’re not just embracing automation; we’re driving its adoption in ways that benefit our clients and the industries we serve. By continuing to explore how automation can complement and elevate the principles of metal spinning, we aim to lead the way in delivering precise, efficient, and built solutions for the future.
The future of metal spinning is here, and it’s automated. Let’s shape it together.